8 Packaging Optimization Strategies for Supply Chain Efficiency
In supply chain operations, packaging optimization emerges as a key player in reshaping how businesses tackle logistics challenges. Packaging optimization has become a strategic ally, contributing to streamlined operations and cost reduction. However, optimizing packaging isn’t just a cost-cutting measure; it’s a commitment to operational excellence.
Packaging optimization strategies paint a bigger picture of efficiency, cost-effectiveness, and sustainability—a narrative of success in the realm of supply chain management.
For instance, right-sizing packages will not only protect the product but will serve as an opportunity for businesses to reduce waste and optimize resources. The integration of smart track and trace systems provides heightened visibility, providing real-time insights into the location and condition of each package.
This article will explore various practical packaging optimization strategies for a more resilient supply chain.
What is Packaging Optimization?
Optimization in packaging is a strategic approach that involves the calibration of packaging elements to maximize efficiency, protection, and cost-effectiveness within the supply chain. It is a comprehensive analysis and enhancement of packaging processes, materials, and designs to align with the goals of the business and broader market trends.
Achieving the optimal balance among these elements requires a nuanced understanding of the product’s nature, the intricacies of logistics, and the evolving landscape of consumer expectations.
The Benefits of Packaging Optimization
The primary objectives of packaging optimization include reducing operational costs and enhancing overall supply chain performance.
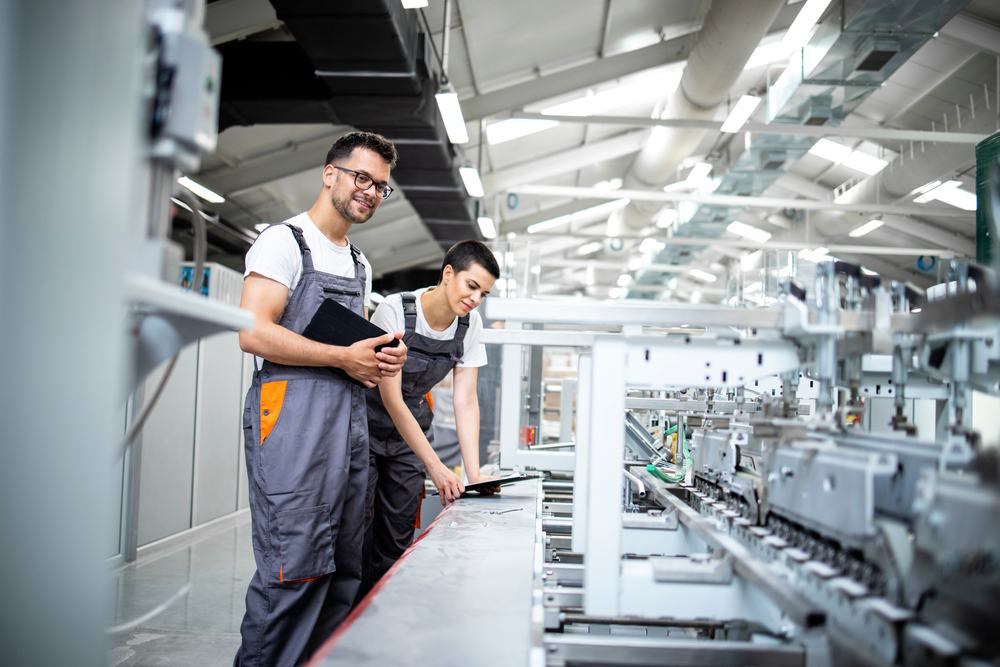
However, packaging optimization benefits ripple across the entire supply chain, from streamlined operations to enhanced brand reputation in an environmentally conscious market. Here are some of its specific advantages and goals:
Efficiency enhancement | – Streamlining packaging processes for faster handling and shipping – Minimizing delays and bottlenecks within the supply chain |
Supply chain resilience | – Strengthening the supply chain against external disruptions – Increasing resilience to challenges such as natural disasters, economic fluctuations, or global crises |
Cost reduction | – Identifying opportunities to cut packaging costs without compromising quality – Reducing excess material usage and minimizing waste in the packaging process |
Improved product protection | – Ensuring products reach their destination in optimal condition – Mitigating damages during transit through strategic packaging design |
Adaptability to market changes | – Creating packaging solutions that can flexibly adapt to changing market demands – Nimbly adjusting packaging configurations in response to evolving consumer preferences |
Sustainability | – Incorporating eco-friendly materials and practices to reduce environmental impact – Meeting consumer demands for sustainable packaging solutions |
Regulatory compliance | – Ensuring that packaging aligns with regulatory standards and requirements – Mitigating risks associated with non-compliance through meticulous packaging design |
Packaging Optimization in the Supply Chain: 8 Strategies
Packaging optimization in the supply chain not only enhances operational efficiency but also aligns businesses with evolving market expectations, positioning them as leaders in responsible and forward-thinking logistics practices. The following are packaging optimization strategies to consider for supply chain efficiency.
1. Right-size your packaging
Right-sizing allows you to tailor the dimensions of your product packaging to fit the requirements of the shipped product precisely. The goal is to minimize excess space and material while ensuring optimal protection for the goods throughout the supply chain. It strikes a balance between the size of the packaging and the dimensions of the product, eliminating unnecessary voids and packaging waste.
Equip your supply chain with cutting-edge tools and technologies that continuously optimize package dimensions. Implement software solutions that analyze shipping trends, order sizes, and destination specifics to adjust packaging parameters dynamically. This ensures an ongoing commitment to efficiency and cost-effectiveness in your packaging processes.
2. Utilize eco-friendly materials
Stay at the forefront of sustainability by exploring and adopting cutting-edge sustainable materials for packaging. Consider using biodegradable, compostable, or post-consumer recycled (PCR) materials. For instance, replace traditional plastic packaging with innovative alternatives made from plant-based materials to reduce environmental impact. Beyond the ecological advantages, these materials often weigh less, potentially reducing shipping costs and enhancing overall supply chain efficiency.
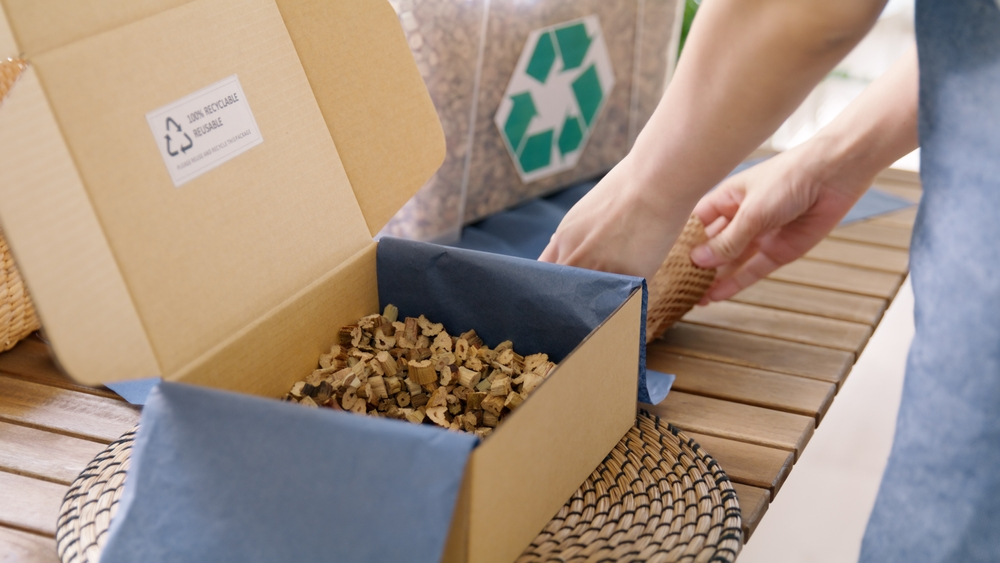
Overall, the use of sustainable materials can lead to reduced material expenses, lower waste disposal costs, and potentially lighter packaging that contributes to decreased transportation expenses. Moreover, this strategic choice contributes to an enhanced brand image, showcasing your commitment to responsible business practices and appealing to environmentally-conscious consumers.
Seamlessly integrating eco-friendly designs into packaging solutions requires collaborative strategies with suppliers and designers. Work closely with a sustainable packaging manufacturer to redesign packaging with minimal material while maintaining product integrity. This approach also optimizes space utilization, leading to reduced packaging costs.
3. Deploy smart track and trace systems
Advanced track and trace systems can ensure precise monitoring of shipments throughout the entire logistics process. Utilizing GPS and sensor technologies enhances accuracy, provides better control over your supply chain, and empowers your organization with increased responsiveness to potential disruptions.
Beyond mere tracking, this enhanced visibility enables proper decision-making, optimizing the flow of goods and minimizing the impact of unforeseen events on your operations. The ability to monitor shipments with precision also allows for more efficient allocation of resources, reducing unnecessary expenditures and enhancing the cost-effectiveness of your logistics processes.
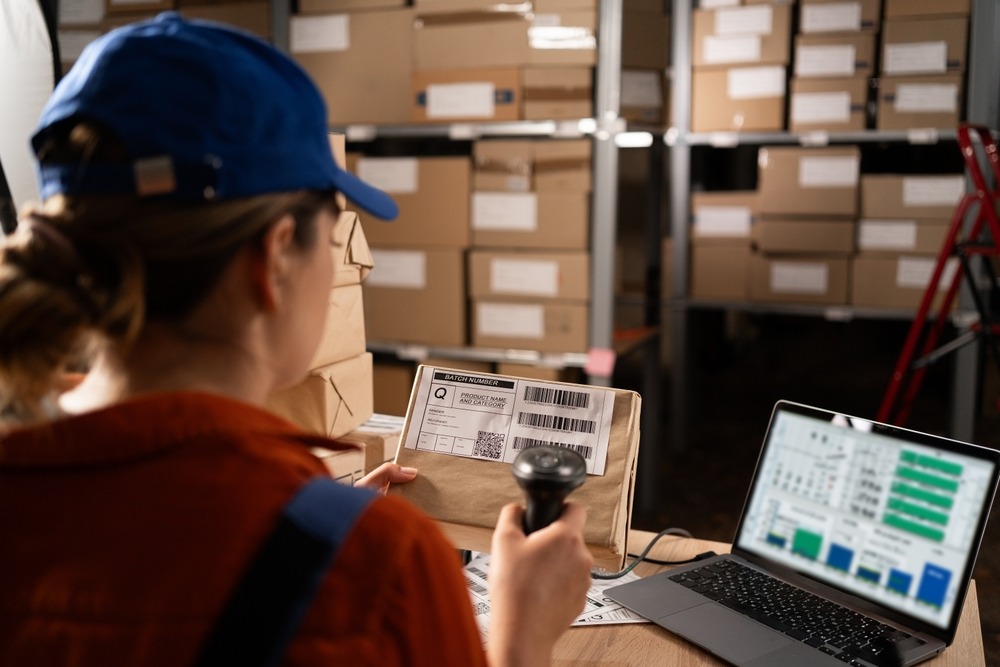
For example, strategically tagging products with RFID chips and leveraging IoT devices provides comprehensive insights into the location and condition of each item. This not only streamlines inventory management but also serves as a catalyst for proactive decision-making based on real-time data.
With these levels of visibility, your organization can address potential bottlenecks, minimize delays, and optimize routes. This strategic use of technology also enhances customer satisfaction by ensuring timely and accurate deliveries.
4. Implement precision labeling and barcoding
Implementing high-precision labeling on your packages can significantly reduce errors in sorting and shipping, fostering smoother supply chain operations. For example, labels produced with precision are easily scanned and interpreted by automated systems, minimizing the likelihood of misreads or delays. This improves the reliability of your supply chain and contributes to cost savings by reducing the need for manual interventions and mitigating potential errors during transit.
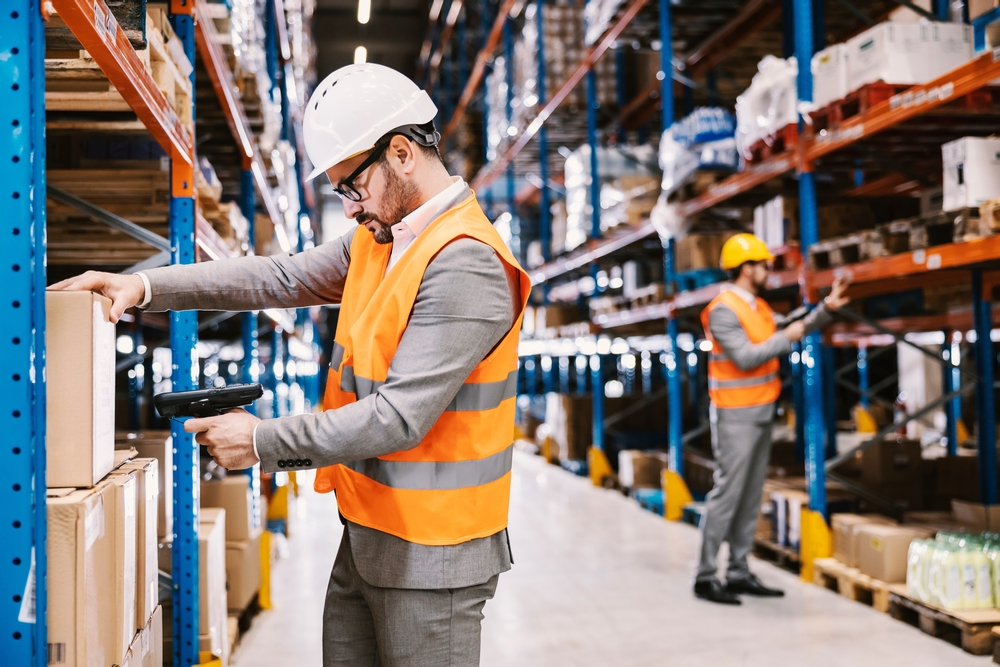
Utilizing QR codes, in particular, elevates the amount of information stored on each item, ensuring accuracy in tracking inventory levels. This integration facilitates more sophisticated data-driven decision-making throughout the supply chain. With a robust barcode system, real-time visibility into stock levels allows for better demand forecasting, optimized storage space, and improved overall resource allocation.
5. Foster collaborative supply chain packaging design
Creating collaborative design partnerships with suppliers is instrumental in optimizing packaging across the supply chain. By working together, your organization can create packaging solutions that meet both product protection and logistical efficiency goals.
For instance, collaborating with a reputable packaging converter can lead to innovative designs that reduce material waste without compromising product integrity. This collaborative approach not only enhances sustainability but also ensures that packaging solutions are tailored to the unique requirements of your supply chain.
This collaborative effort also involves sharing insights, best practices, and data to identify areas of improvement. Joint initiatives foster a holistic approach to packaging optimization, ensuring that strategies are cohesive and responsive to the diverse needs of the supply chain.
6. Integrate reusable packaging
Reusable packaging not only contributes to reducing waste but also yields cost savings. For instance, using durable, returnable packaging for shipping goods between distribution centers significantly decreases the need for single-use materials.
Establishing efficient reverse logistics processes to retrieve and refurbish reusable packaging also ensures a closed-loop system. Implementing a tracking system for reusable packaging adds accountability and helps maintain the integrity of the materials throughout their lifecycle. Seamless integration not only supports environmental sustainability but also ensures a smooth transition that minimizes disruptions in supply chain operations.
7. Automate the packaging process
Improving packaging efficiency is achievable through strategic investments in state-of-the-art automated packaging systems. Automating repetitive tasks in the packaging process, such as picking and packing, enhances speed, accuracy, and consistency.
Deploying robotic arms can significantly reduce labor costs while increasing throughput. Utilizing robotic systems for tasks such as palletizing, labeling, and sorting also reduces the risk of human error in the packaging process. This investment improves operational efficiency and positions your organization to respond effectively to fluctuating demands, ensuring a more agile and cost-effective supply chain.
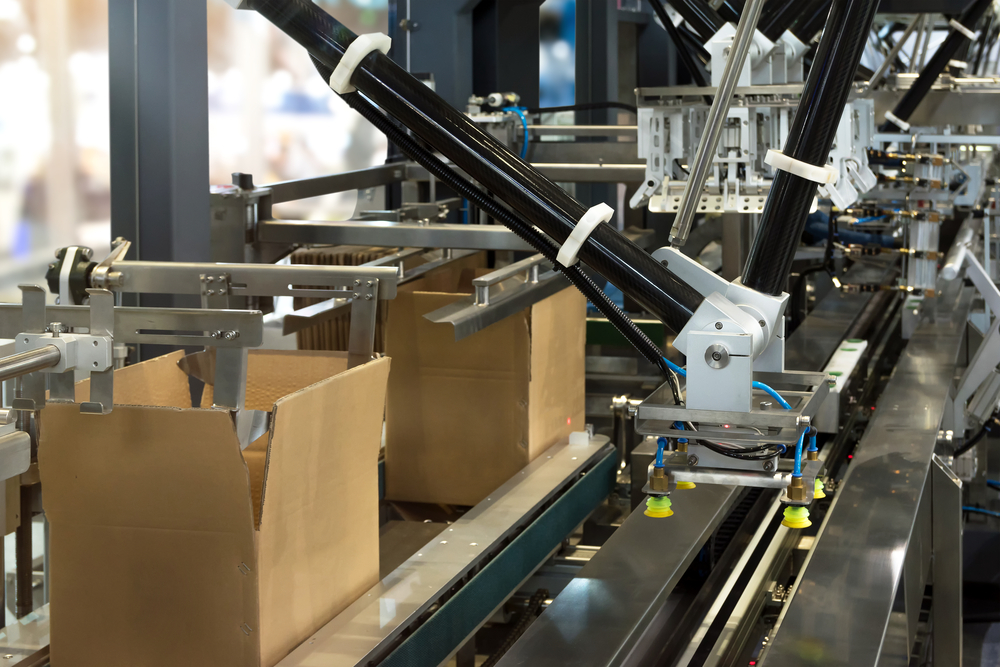
8. Make data-driven packaging decisions
Optimize packaging configurations by utilizing advanced data analytics. Analyze historical data, shipment patterns, and customer preferences to identify opportunities for improvement.
Understanding the performance of different packaging options over time allows your organization to refine and optimize the packaging strategy continuously. Learning from past successes and challenges positions your supply chain to be more responsive and adaptable.
Data analytics can also reveal trends in order sizes, allowing you to adjust packaging dimensions accordingly for more cost-effective and eco-friendly solutions. This contributes to enhanced cost efficiency and customer satisfaction.
Sealing Supply Chain Success: Strategic Packaging Optimization
Packaging optimization is a strategic imperative for brands seeking to elevate their supply chain efficiency, reduce costs, and streamline operations. These are essential to stay competitive and agile in a dynamic business and global logistics landscape.
As brands continue to embrace these strategies, they position themselves at the forefront of a more resilient and environmentally conscious supply chain future.
For comprehensive packaging solutions tailored to your supply chain needs, Meyers is your trusted custom packaging company committed to innovation, sustainability, and client success. Discover how the packaging experts at Meyers can elevate your packaging strategies, optimize your supply chain, and drive long-term success in the ever-evolving market.